Geogrids: A different way of thinking
by Jonathan Cook, on January 16, 2020
Cement and chemical stabilisation is not the only green and cost-effective alternative to dig and replace for delivering a robust and long-lasting roads network.
Two of the central pillars of the UK Government’s Road Investment Strategy are to reduce maintenance costs by 30-50%, compared with current levels, and to reduce the environmental impact of the road network.
The green roads agenda
The green roads agenda will, of course, be achieved by reducing carbon emissions of vehicles and also by building-in environmental measures to all new schemes – and rectifying environmentally-poor designs when repairing, maintaining and upgrading existing roads.
Geotechnics has a lot to offer in this regard, particularly when building new roads over weak and/or waterlogged ground. Thankfully, today’s engineers are less likely to resort to the traditional approach of dig and replace and will consider a number of different approaches to increase bearing capacity, that are not only faster and more cost-effective but that are greener too – such as chemical stabilisation and the use of soil stabilisation geogrids.
The limitations of chemical stabilisation
While chemical stabilisation – using lime, cement and other hydraulic binders – can reduce environmental impact by reducing the amount of material having to be disposed of, and the amount of imported material needed (with the associated reduction in lorry movements), the method does have its limitations.
Chemical Stabilisation being applied
For a start, not all soils are suitable for chemical stabilisation – the method is most effective on high plasticity clays, silts and fine sands – and soils containing sulphates can react negatively to the binder. Testing is needed to confirm suitability prior to treatment and the ground needs to be left to cure for a few days afterward, before construction can continue. There is also a risk of the treated soil deteriorating if there are frequent wet-dry cycles, which can lead to cracking.
Additionally, stabilisation plant and equipment is heavy, making it difficult to reach the areas with the softest soils, and treatment cannot be carried out in heavy rain.
Tensar geogrid: fast, simple and cost-effective
Installing Tensar geogrid in a capping layer or in the unbound layers of a road pavement, on the other hand, is often faster, simpler and more cost-effective and delivers significant improvements in bearing capacity.
Up to £2m was saved on the construction of the A556 improvement scheme in Cheshire by using Tensar geogrid to mechanically stabilise the new road’s founding aggregate layers.
An aggregate layer stabilised with Tensar geogrids performs as a composite, due to the interlocking mechanism and particle confinement that develops between the aggregate and the geogrid. This Tensar ‘mechanically stabilised layer’ provides more effective support to the entire pavement structure than aggregate alone.
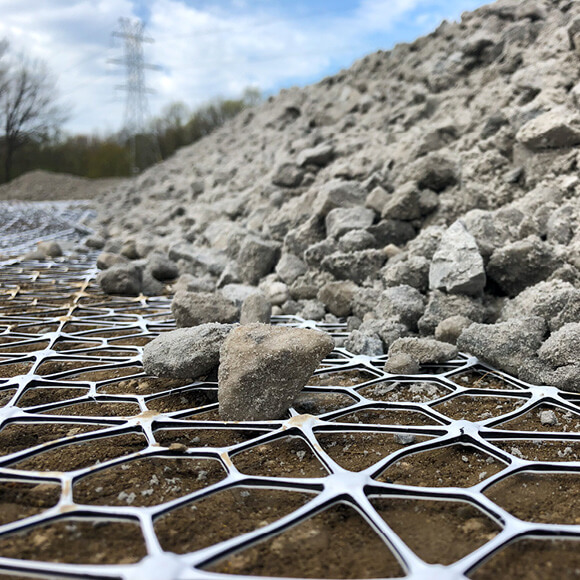-(1).jpg)
Tensar InterAx interlocks with aggregate particles to create a mechanically stabilised layer.
Spectra Pavement Optimisation
Tensar’s flexible road pavement designs use Tensar InterAx geogrid, as part of the Tensar Spectra Pavement Optimisation system.
This is a tried and tested approach, accepted by many highways authorities around the world, to provide longer lasting sustainable road pavements.
Tensar Spectra Pavement Optimisation saved £0.5m, reduced material use by 7,000t and cut three weeks off construction of the Finningley and Rossington Regeneration Route Scheme in Yorkshire, plus increased road service life by 60%.
Tensar geogrids can be used with every soil type, there are no requirements to assess suitability and they can be installed by hand, without specialist skills, in any weather. Plus there is no ‘curing time’: construction of the road pavement can proceed immediately.
The environmental benefits of geogrids
From an environmental point of view, like chemical stabilisation, Tensar geogrids can reduce the amount of unsuitable material that has to be excavated and, in some cases, remove the need entirely.
They can also be used with recycled, site-won marginal fills and help reduce the thickness of aggregate layers (and hence use fewer materials), while improving overall pavement performance.
Tensar TriAx geogrid enabled construction of access roads over very weak peat at the Glenchamber Wind Farm in Scotland.
Of course, there is no getting away from the fact that geogrids are made from plastic but it is important to note that the polypropylene used in their manufacture is chemically-inert, does not degrade and can be recycled at the end of a road’s operational life.
Delivering robust and long-lasting infrastructure
Full-scale field testing has demonstrated that mechanically stabilised aggregate layers deliver more robust and longer-lasting road pavements, increasing traffic capacity by up to six times that of traditional designs.
This will obviously help reduce the maintenance and repair burden on owners and operators, further strengthening the argument that geogrids should be at the heart of helping to meet the Government’s drive for a roads network that is greener, sustainable and delivers value for money.