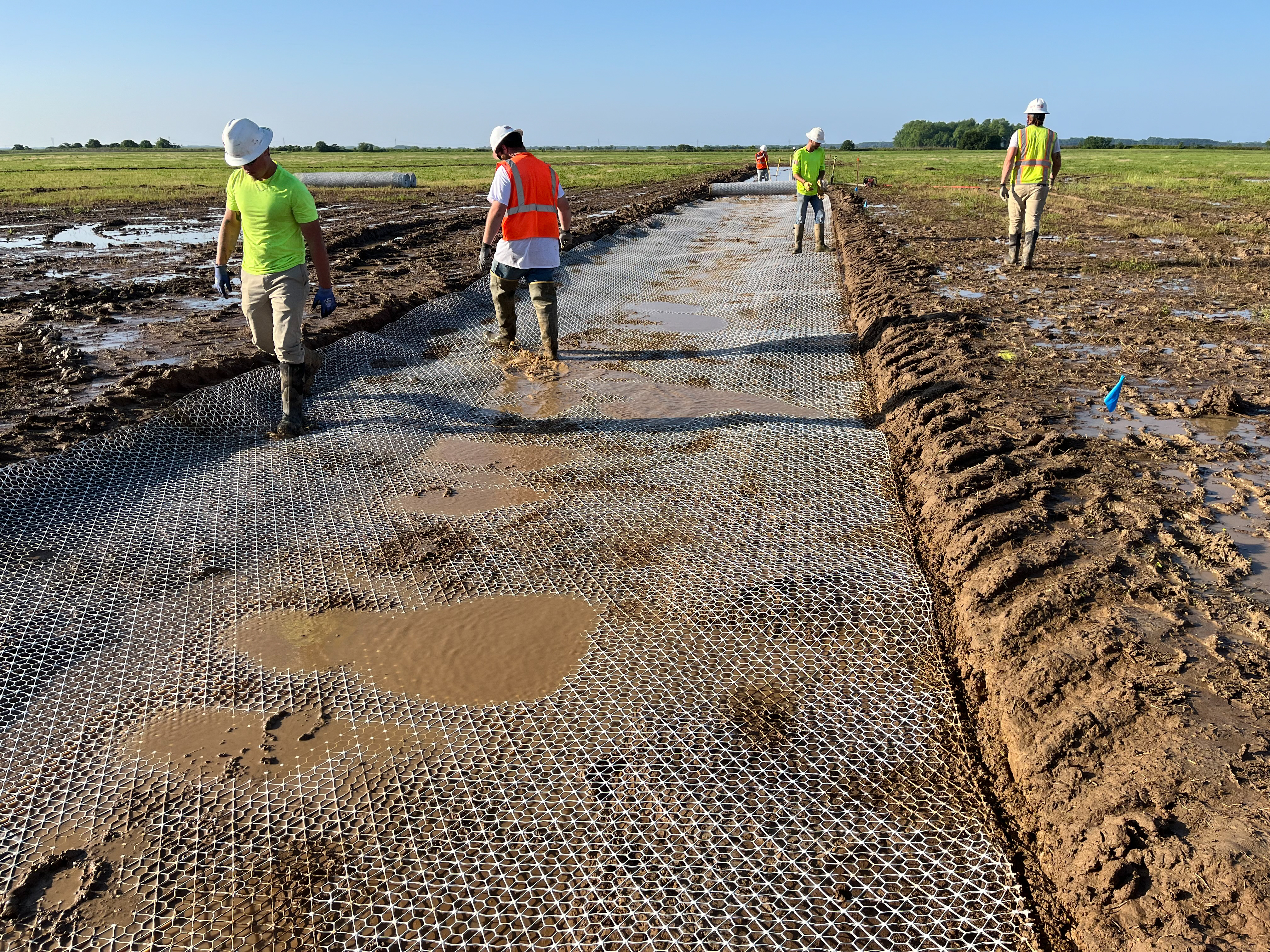
InterAx vs Biaxial Field Test
A large, national General Contractor was constructing haul roads to support a large industrial project. To reduce aggregate thickness and minimise maintenance, the project team incorporated Tensar InterAx geogrid into the road design. Prior to construction, the contractor was approached by another geogrid manufacturer with claims that their high-strength biaxial geogrids with a nonwoven fabric attached, could provide the same performance as InterAx at a lower price. The contractor decided to stage a side-by-side in-ground test to compare performance of the different products, under comparable subgrade conditions, aggregate fill thickness, construction practices, and traffic loading.
Conclusions
- The Tensar InterAx section outperformed both biaxial geogrid sections.
- Geogrid material properties, such as tensile strength and stiffness, are not
predictors of performance.
Before the installation began, around 35mm of rain fell on the site during a thunderstorm. The next day, excavation and dewatering of the site took place before the installation of the three geogrids and placement of a layer of “100mm down” dense graded aggregate (DGA) fill over the geogrids. A week later, they placed a further layer of “37.5mm down” DGA and then static rolled the sections. The three completed test sections were all trafficked 50 times by the same fully loaded dump truck. Each time, the truck made a straight pass over the entire 90m of test sections, then exited the haul road, looped around, and drove over the test sections again the same way. After trafficking was complete, the contractor identified and measured the worst rutting in each 30m test section.
The rutting measurements taken after trafficking the sections were significantly less for the section built with Tensar InterAx than for either of the two sections built with biaxial geogrids. In the first section, built with InterAx underneath, 50 passes with the loaded dump truck only produced around 12mm of rutting. The second and third sections, on the other hand, constructed using the biaxial geogrids, rutted by around 60mm and 100mm, respectively. Rutting measurements were representative of the average rutting experienced in each test section.
Each of the three constructed test sections were built to the same design: a geogrid product covered first with 125mm of the “100mm down” DGA and then topped with an additional 75mm of the “37.5mm down” DGA.