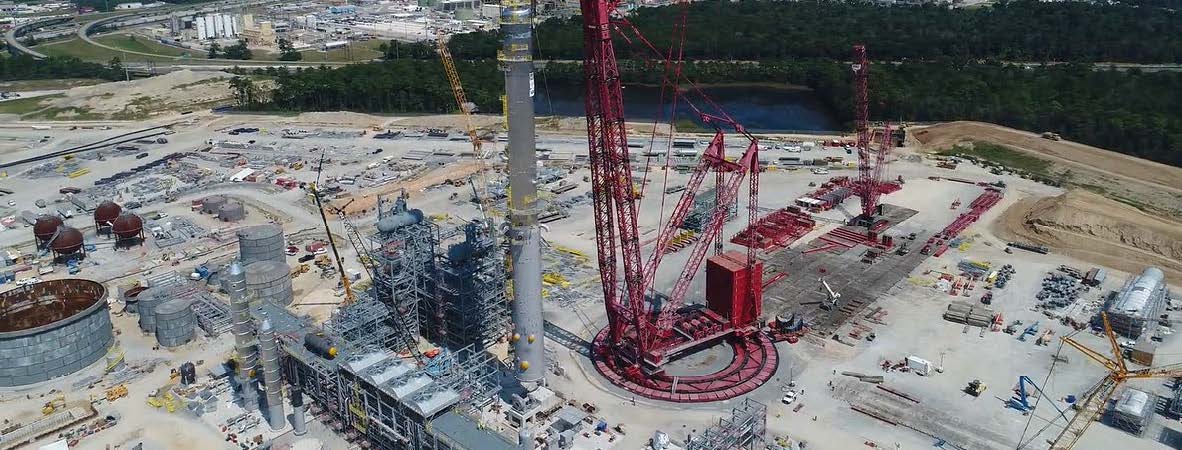
Petrochemical Crane Project
Significant Cost and Time Savings Achieved for Crane Pad Designed with TensarĀ® Geogrid.
Design and construction of a geogrid stabilized working platform for use with a ringer crane in the US was undertaken in 2016 and completed in 2017. Problematic soil conditions were found at the crane pad area and consisted of fat clays and occasional sandy silt lenses and pockets. The vertical soil profile showed five different CH layers comprising nearly 50% of the soils. The ringer crane was configured with a maximum bearing pressure of 192 kPa, a load Spreader ring with outside and inside diameters 56 m and 33.2 m, respectively, and was rated the third largest in the world. Stringent criteria for differential and total settlement needed to be met to ensure successful crane operation. Heavy seasonal rains were impacting construction.
A multi-axial geogrid-stabilized working platform was designed to
improve allowable bearing capacity of the soil and to decrease potential settlement.The crane bearing pad was installed on time and on budget despite of numerous construction delays due to the heavy seasonal rains. Unlike the concrete option that was considered, the crushed stone could be easily removed and reused at other site locations. This resulted in a cost savings of at least $2.3 million.
Estimated total cost savings of $3.1 Million when compared with original plans to construct a deep foundation system. Success of the geogrid stabilized platform was further demonstrated when it withstood Hurricane Harvey without damage and the crane was back in operation the day after the storm passed.