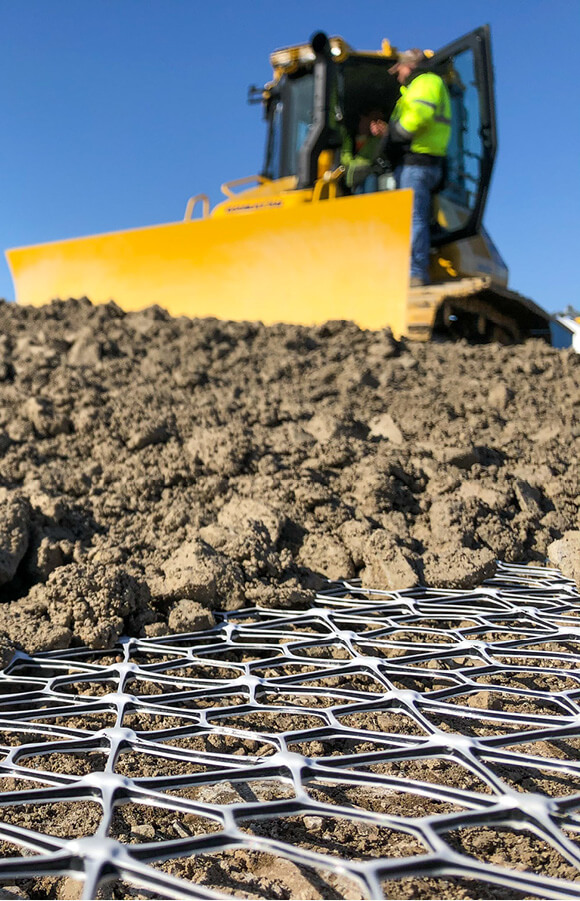
Geogrids
Solution Overview
A geogrid consists of a 2-dimensional arrangement of integrally connected tensile elements or ribs that form a grid or net-like structure, usually supplied in roll form. Manufactured from polymers, geogrids are classed as geosynthetic products; this is a broad product classification that includes geotextiles and geomembranes alongside other minor categories.
Tensar geogrids are typically manufactured from oriented high-density polyethylene (HDPE) or polypropylene (PP) for durability, stiffness and strength. The junctions between ribs are integrally formed giving them high strength and structural stability. The design quality and effectiveness of Tensar geogrids has made them the go-to solution for local authorities in the UK and around the world.
Polymeric geogrids are used to solve civil and geotechnical engineering problems in or on the ground. They primarily provide soil stabilisation or reinforcement function, to add to or enhance the properties of soil or aggregate materials.
Geogrids were invented by our company founder, Dr Frank Brian Mercer, who patented his design in 1978. Since then, Tensar has been at the forefront of product innovation globally and manufactures the most advanced solution on the market – Tensar® InterAx®.
Geogrids Products & Systems
There are no results that match your search. Please try another search or Contact Us with further questions.
What is geogrid?
Geogrid is a type of geosynthetic material that provides a stabilisation and reinforcement function to aggregates and soils. The design comprises a two-dimensional pattern of ribs to form a series of apertures or open spaces, enabling geogrid to stabilise and reinforce earth materials.
What are geogrids used for?
Geogrids primarily provide a stabilisation or reinforcement function, to enhance the performance of soils. They also provide separation between soil and aggregate layers and are used widely in civil engineering applications.
Geogrids can be used for the following applications:
- Building stable working platforms over soft ground conditions
- Enhancing the service life of roads, pavements and trafficked areas
- Improving the long-term performance of paved and unpaved roadways by minimising aggregate movement
- Reinforcing soil walls
- Foundation and embankment support
- Railway trackbed improvement
How does geogrid stabilisation work?
Geogrids work efficiently because the apertures between ribs allow the aggregate to strike through and interlock with the geogrid. Provided the geogrid is stiff enough, the rib profile deep enough and the junctions strong enough, earth materials are confined within the apertures to prevent the movement of aggregate. This forms a new geogrid/aggregate composite material with improved strength and resistance to deformation.
How do geogrid solutions reinforce soils?
For soil reinforcement geogrid applications, load must be transferred between the soil and the geogrid. The transverse ribs of uniaxial geogrids provide an efficient mechanism for load transfer by abutment rather than friction alone. The high tensile load in the geogrid is carried by the longitudinal ribs. They must be capable of sustaining such high loading for the full life of the structure (often up to 120 years), requiring durability and long term strength and stiffness.
What are the types of geogrids?
The main types of geogrids are the following: uniaxial geogirds, biaxial geogrids, triaxial geogrids (TriAx®), Tensar H Series (HX) geogrids and Tensar InterAx® geogrids.
Who invented geogrids?
Geogrids were invented by Dr Frank Brian Mercer and patented in 1978. Prior to its acquisition, Mercer founded the company Netlon which went on to become Tensar. Continuing the tradition of innovating geosynthetics, Tensar still stands today as the world leader in geogrids, investing in the research and development of new products such as Tensar® InterAx®.
To learn more, see our booklet on Dr Frank Brian Mercer and the invention of polymeric geogrids.
Comparing Tensar Geogrids with alternative soil reinforcement solutions
The efficiency of the interlock and confinement provided by a geogrid is dependent upon its physical characteristics (in-plane stiffness, junction efficiency, rib profile) and compatibility with the aggregate (particle size and type). Different geogrids with the same short term QC strength can have widely different characteristics dependent on the method of manufacture, the joint type, rib profile and polymer used.
For soil reinforcement applications, the geogrid mesh must have proven long-term strength and stiffness characteristics as well as high durability. Geogrids vary in their long-term characteristics, dependent upon the manufacturing methods and the polymer used. Tensar uniaxial geogrids are certified for 120-year design life in a wide range of soil pH and chemically aggressive environments.
See below how Tensar’s geogrid solutions directly compare to other geogrids and ground reinforcement products.
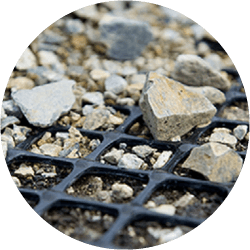
Generic Biaxial Geogrids
- Products suited to bi-directional reinforcement
- Lower confinement efficiency due to effect of rib profile or lower junction strength provides reduced performance
- Design parameters typically based on small scale testing, or geogrid properties
- Typically not proven for use in road base, primarily utilised over weak ground
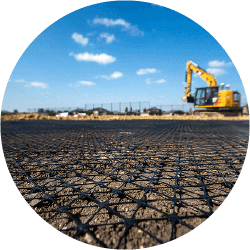.png?lang=en-AU)
Tensar® Geogrid
- Products optimised for mechanical stabilisation of aggregates
- Highly efficient aggregate confinement increases bearing capacity and limits surface deformations
- Design parameters developed from full-scale accelerated trafficking tests of mechanically stabilised layers
- Proven suitability for base stabilisation in permanent roads as well as road foundations over weak ground
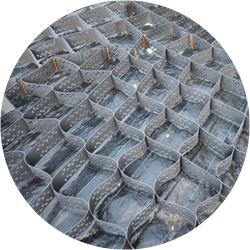.png?lang=en-AU)
Geocell
-
Aggregate or sand fill confined by cell walls to increase bearing capacity. Difficult to achieve compaction within cells
- Complex installation requires more labour and time to open, secure and place first layer. Fill is difficult over weakest soils
- Typically limited to installation over soft soils
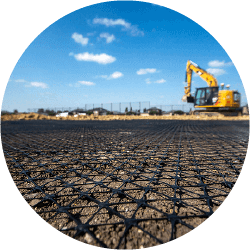.png?lang=en-AU)
Tensar® Geogrid
- Highly efficient aggregate confinement creates a mechanically stabilised layer with improved bearing capacity. Aggregate compaction is enhanced
- Installation costs are low. Quick and simple to roll out and commence fill. Over very weak soils access is made possible by ‘snowshoe effect’
- Proven suitability for base stabilisation in permanent roads to increase pavement life as well as for road foundations over weak ground

Geotextile Reinforcement
- Mobilisation of geotextile strength to reinforce aggregate is limited by friction
- Load support is developed by the tensioned membrane mechanism requiring higher surface deformation to mobilise the reinforcement effect
- Typically limited to installation over soft soils where surface rutting is permissible
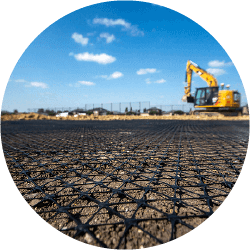-(1).png?lang=en-AU)
Tensar® Geogrid
- Product design optimised for mechanical stabilisation of aggregates by interlock and confinement
- Highly efficient aggregate confinement by interlock increases bearing capacity and limits surface deformations
- Proven suitability for base stabilisation in permanent roads to increase pavement life as well as for road foundations over weak ground where surface rutting is to be limited
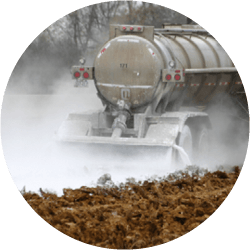.png?lang=en-AU)
Chemical Stabilisation
- Large equipment required for treatment. Difficult access over very weak soils. High mobilisation and set up costs limit use to larger area projects
- Limited to use with certain soil types and unsuitable for organic and certain clay soils
- Windblown dust can be an issue during installation. Drainage and hydrology of soil is affected.
.png?lang=en-AU)
Tensar® Geogrid
- Installation costs are low. Quick and simple to roll out and commence fill. Over very weak soils access is made possible by ‘snowshoe effect’. Suitable for projects of any size
- Mechanically stabilised layers can be used over all soil types including organic soils
- Mechanical stabilisation has minimum environmental impact during installation and when in-place. Suitable for end-of life excavation and disposal
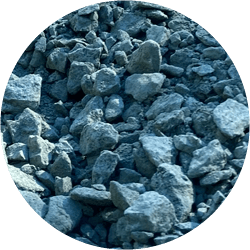.png?lang=en-AU)
Non-Stabilised
- Weak soils required to be excavated and disposed off-site, then backfill with suitable materials prior to placement of aggregate layers. Resulting in increased traffic movements, project costs and carbon emissions
- Thicker layers of aggregate required to achieve the same bearing capacity and surface rutting profile. Resulting in higher construction cost, increased time and greater carbon emissions
- Increasing pavement life would require an increase in thickness of the unbound layers, increasing overall costs, materials usage, and carbon emissions
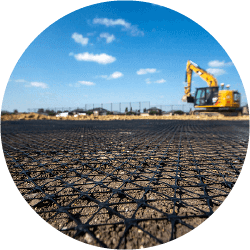-(1).png?lang=en-AU)
Tensar® Geogrid
- Allows installation, placement, and compaction of aggregate layers over very weak and variable soils
- Mechanical stabilisation enables reductions in capping layer or subbase thickness over weak or variable soils
- Mechanical stabilisation of unbound layers in permanent roads increases pavement life or enables pavement layer thickness to be reduced for the same life
Free-Draining Separation Barrier
Testing and experience have shown that Tensar geogrids support the function of separation when properly graded aggregate fill is used. Our geogrids are not prone to “blinding out” or clogging which may occur with a geotextile used as a separation layer.
Trenching with geogrid
Tensar geogrids are routinely excavated through and punched through in order to place underground utilities.
How are geogrids made?
Geogrids mesh products are typically made from polymer materials, including polyester, polypropylene, polyethylene, or polyvinyl alcohol. They can be woven or knitted from yarns; punched into a polymer sheet; extruded through rotating die heads to create a net structure or welded from strips of material.
Punched and drawn geogrids
Molten polymer is extruded into a sheet of defined thickness and a pattern of holes is punched into the sheet. The punched sheet is then stretched in either a single direction to form a uniaxial geogrid or in two directions to form either biaxial or multi-axial geogrids.
Extruded geogrids
Molten polymer is extruded through rotating “die heads” each with a series of “holes” which allow the creation of a “net” type structure. The geometry of the resulting net or geogrid is dependent on the die/extrusion configuration with both uniaxial and biaxial products available.
Welded geogrids
Polymer strips are manufactured and are then bonded together to form a square or rectangular grid shape. The bonding would typically be carried out using heat.
Woven geogrids
Woven geogrids are fabricated by weaving polymer yarns together, or sometimes knitting polymer yarns together to form a net/grid-like structure. These woven products are often then coated with other polymer materials such as polyvinyl alcohol (PVC) to form the final woven geogrid.
Geogrid/geotextile composites geogrids
Can be formed by bonding a geotextile separator fabric to the completed geogrid manufactured by the methods above.
It is important to note that whilst the inclusion of a geogrid in a roadway or platform would be expected to have a beneficial effect, these benefits will not be the same for each grade of geogrid product. In fact, research has shown that the manufacturing method can have an influence on the expected performance of the resulting road or platform.
Design with confidence, from anywhere.
- Design & evaluate pavement and gravel sections
- Design & evaluate working platforms
- Easily compare alternative materials
- Determine initial and lifecycle cost savings, time savings, and sustainability metrics
- Create high-level summaries of the design alternatives for project stakeholders
- Share features that aid collaboration
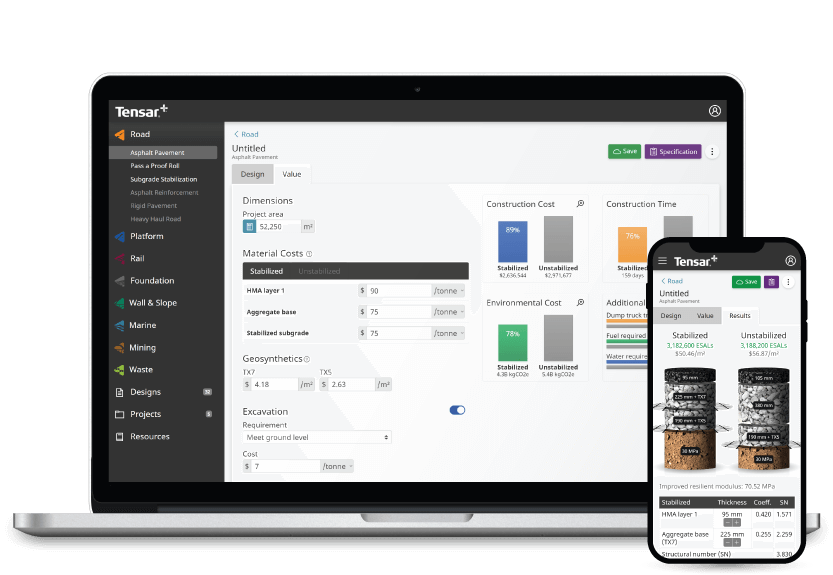
Geogrid Success Stories
Geogrid Resources
Tensar+ Austroads Design Module (Tutorial)
Neuenkirchen Wind Farm - Germany
Check out this incredible footage of Tensar InterAx geogrid being installed at Neunenkirchen Wind Farm in Germany! Here, Tensar InterAx was used for...(Tensar Academy) Webinar Robust Working Platform Design Using the T-Value Calculation Method on Tensar+
Your Regional Sales Manager
Your Inside Sales Manager
Your Local Distributor
There are no results that match your search. Please try another search or Contact Us with further questions.